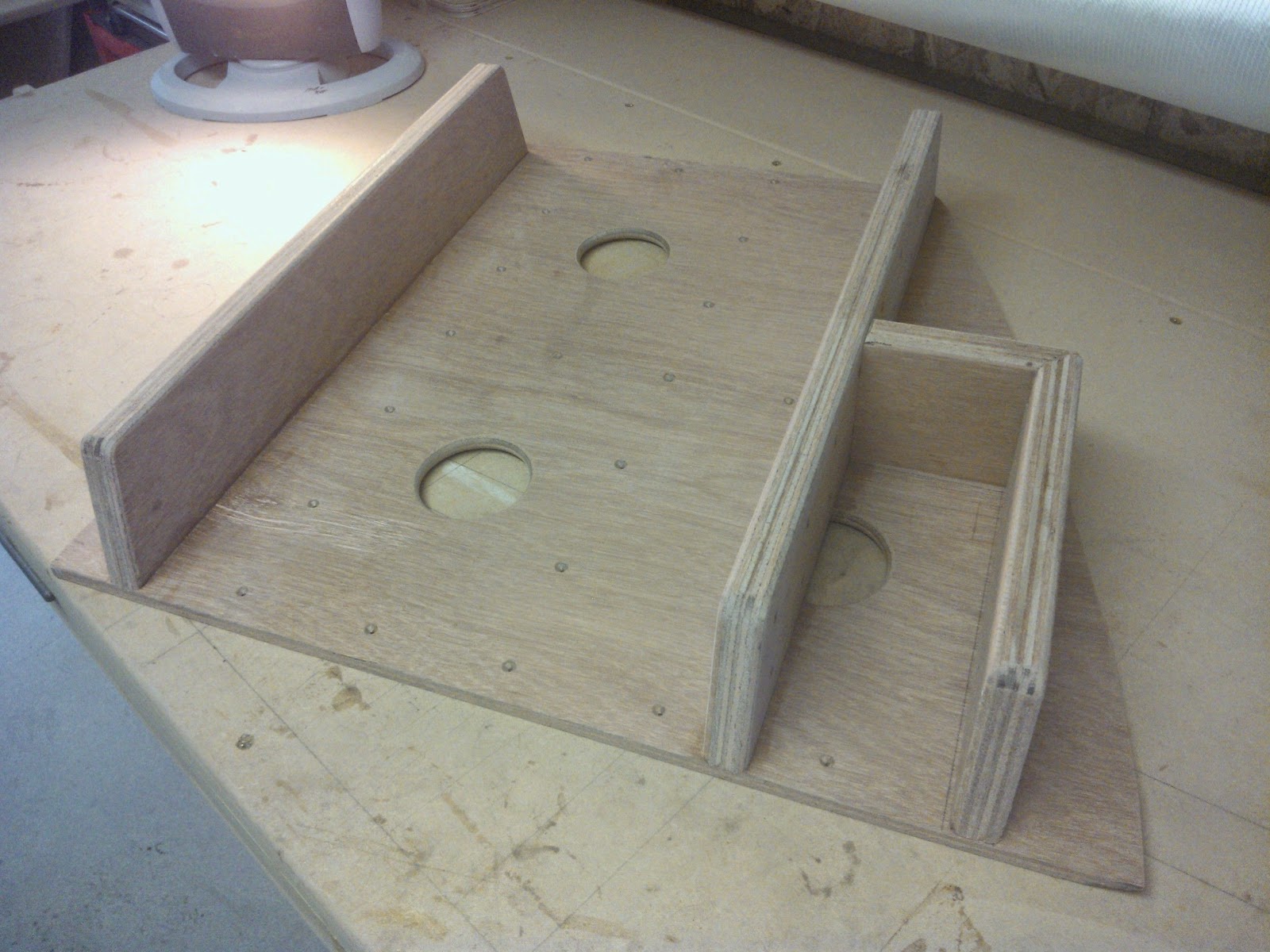
I've come to realise everythings about payoffs in this life; what you do or feel on the one hand may have implications on the other and so as the interest in finishing the boat returns my bank balance and means of replenishing it dwindle away.
Having come to an understanding with myself regarding this projects completion motivates me now but unfortunately i will have to break off to earn some more money to keep it on track. I'm still pricing work all the time yet have none to go to as the level of dickheads.............(sorry, i mean potential customers) that cross my path seem to increase ever more. To clarify; we all get the dreamers, the wafflers and the damn-right dishonest in our work lives but a new category i discovered this week is the 'clueless expert'.
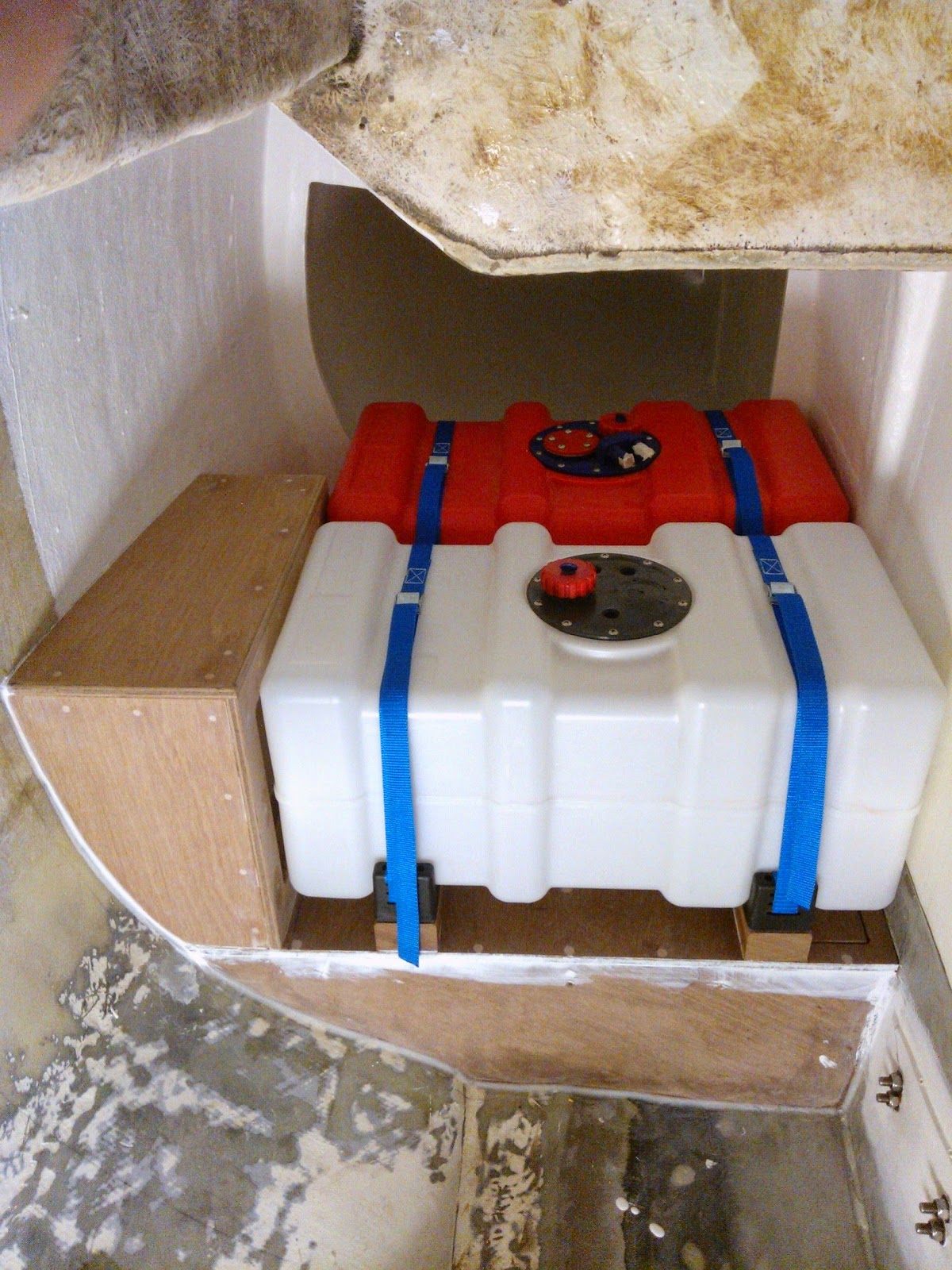
For having no background in my industry a customer told me this week that what i'd conservatively estimated as being a couple of days work could infact be done in four hours, "brilliant, how?" i asked looking them dead in the eye.
"Well you know you lot always over estimate your quotes - dont you?", .......er no actually, i always quote based on hours required to do the work & what the job will entail - if i'm quicker i'll charge you less if something unforseen slows the job up i'll charge more - simple. So the customer eventually agrees abeit reluctantly, everythings cool to come in Monday to start after looking at it Friday night then the texts start Saturday morning, "will it include X?" no because when i asked you you didn't want that, "Will it include Y?" No because you were taking care of that from the conversation we had, "well it has to include 'everything' ".
Sure no problem, i'm thinking more work equals more money but then the text appears on my phone screen "we've had a thought and we're only prepared to go to £150", thats a days money for the extras, okay thats doable but no it turns out thats for the whole job!
So i'm expected to work for nigh on three days driving there and back everyday (45mins each way) burn out cutters and blades on the tools (its a kitchen renovation, new tops, doors etc) use a box or two of screws and gas nails and all for £50 a day.
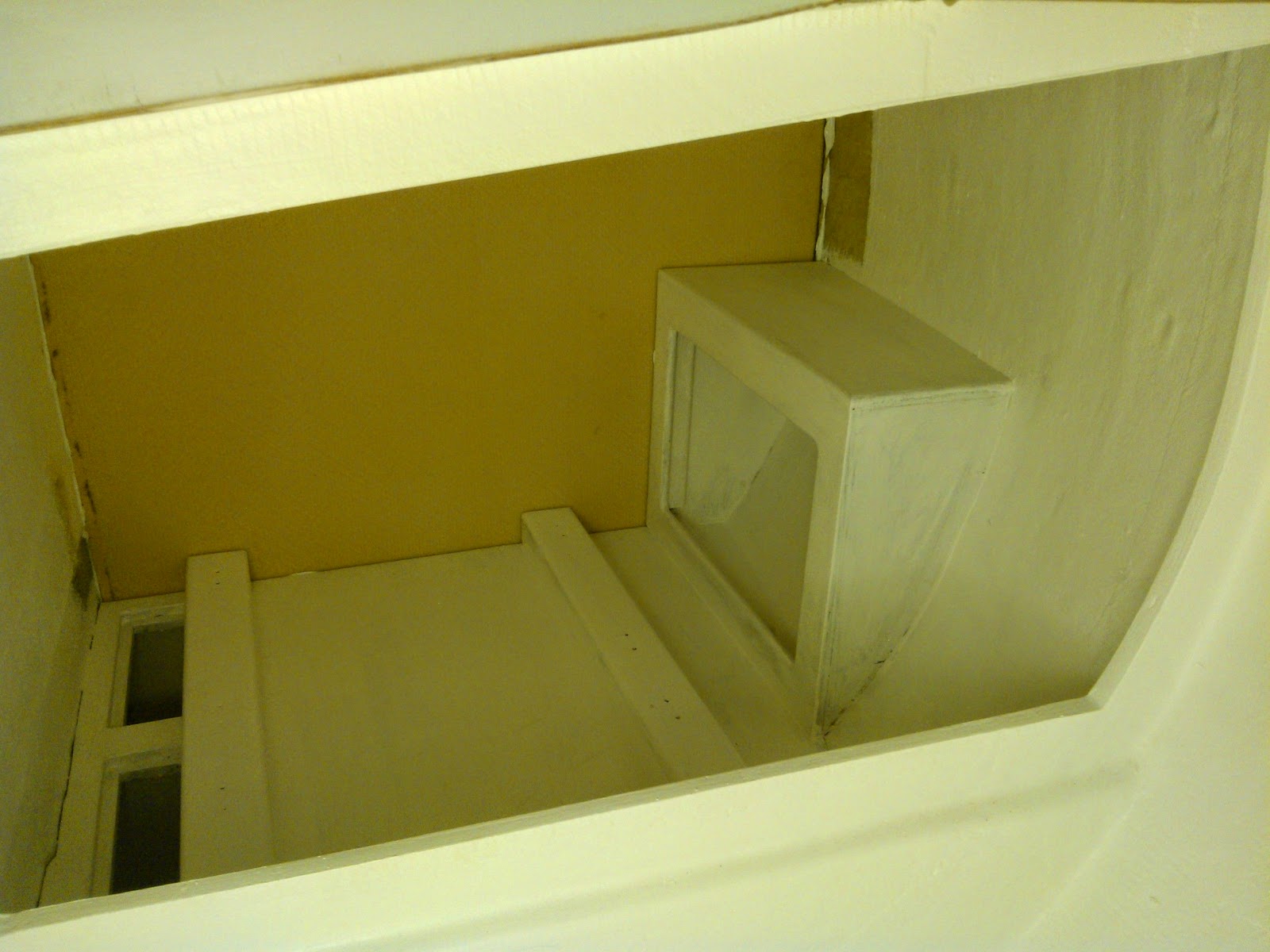
Now I'll do my utmost to swing a job for the sake of a few quid but increasingly this is what i deal with time after time after time - where people treat me like ebay insofar as "we're prepared to go to this figure", but what about the hours, materials, knowledge etc? No apparently you now just pluck a figure out the sky and i'm supposed to bend over and take it. I've had this all year for reasons best known to everyone but me as my day rate is shrinking as i'm aging yet still no work?
Its not much different with the housebuilders too as this austerity 'narrative' that runs through the country is nothing more than a convenient smokescreen for firms to cut everything including what was until a couple of years ago - a livable wage.
Although i've enjoyed working on the boat recently - and i'm not bitter when i say this - i'm quite sure this project will be the last time i use my power tools in anger as i'm completely done with the world of woodworking - the numbers just don't add up anymore.
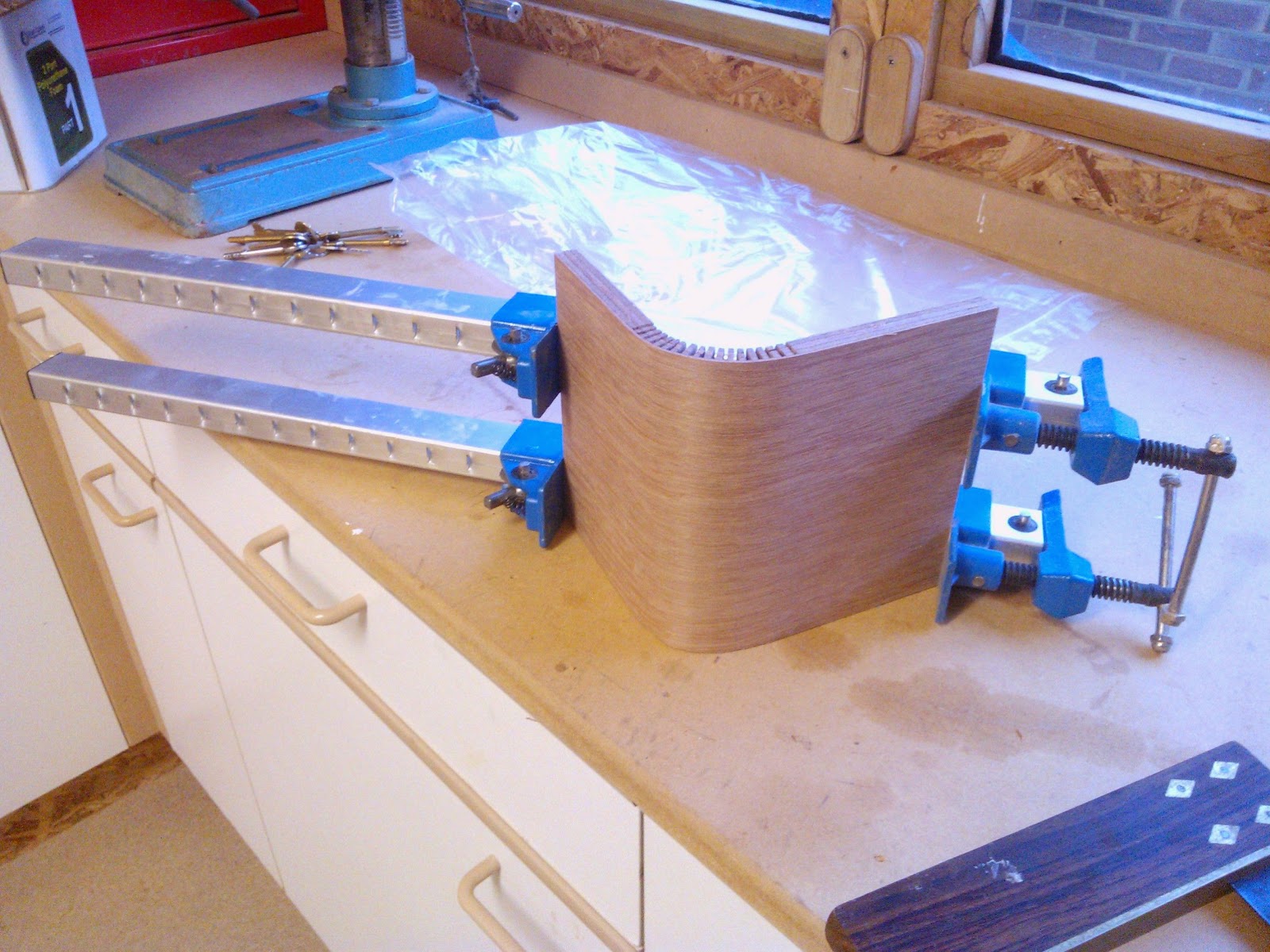
For me 2014 has been the year of the bullshitter where paid works concerned, i'm done dealing with shifty-arse builders, hormonal housewives, and idiot husbands who have not a bloody clue what they're talking about or what it takes to do my job yet seek to tell me how long it'll take and therefore what it will cost.
Still - to the boat - got both the battery and tank compartments fitted out plus spent yesterday fiddling about making a zero clearance insert for the site saw to make my kerfing more accurate, it worked too as i was able to cut and bend a piece of 12mm marine ply through 90 degrees.
The reason being as theres alot of curves still to make inside i can't face going through the foam, ply, epoxy & former nightmare so wil build a simple former to manipulate the wood over it and then using polyester resin set it to that shape.
I say polyester resin as its 'indoors' (galley) and not structural which was always the test for its use and seeing as i have gallons of the stuff plus every additive known to man for it i may as well use it up.