Wednesday, 28 January 2015
Tuesday, 27 January 2015
Cocks Away!!

Then i've got the icebox/fridge freezer next then cooker then to the main bulkhead storage units and nav area, so after i'd looked to the heavens for answers i got the 50mm hole saw out and made provision for the engine inlet and sink outlet.

That was until i saw the glass cores from each hole: Jesus i know i said Westerly' were overbuilt but this is crazy as i know how thin the hull is/was around the cockpit outlets which is only a foot or so back and i know i've added to the layup but these cores are about 15mm thick!

Monday, 26 January 2015
Sunday, 25 January 2015
Written piece
Paid work seems to be fizzling out already so decided to get on veneering the rest of the components pertinent to the companionway, trouble is its below freezing all the time so wasn't entirely surprised to see a few bubbles in a couple of the pieces.
All got sorted with the aid of a steam iron to re-activate the PVA which it did, i then rounded off by getting the first half of the finished floor surface down which went swimmingly so i now have a gentle curve to the floor which i will complete tomorrow and then i can install the seacocks and then the joinery.
Monday, 19 January 2015
Alright just a quick one then.
The engine hatch / companionway steps are the first to get its new coat of oak veneer and looks good on it too:
If i'm not working tomorrow i'll proceed with the rest of the bits i've made, currently got the companionway indoors so it can 'cure' in a dry environment - basically all that means is any areas that aren't stuck down properly will show up quicker so the quicker i can sort. It all went in the vac bag but thats still no gaurantee it'll pull down.
Sunday, 18 January 2015
Futuristic shrubbery.



The plan is to start getting the modules made and clamped in the shop and then dry-fitted onboard although the companionway opening is 800mm at its biggest point so i have to be careful of what can be made outside the boat, the plan is then to get the starboard side in and accomodations made for the relavent appliances.
Saturday, 10 January 2015
Got it!
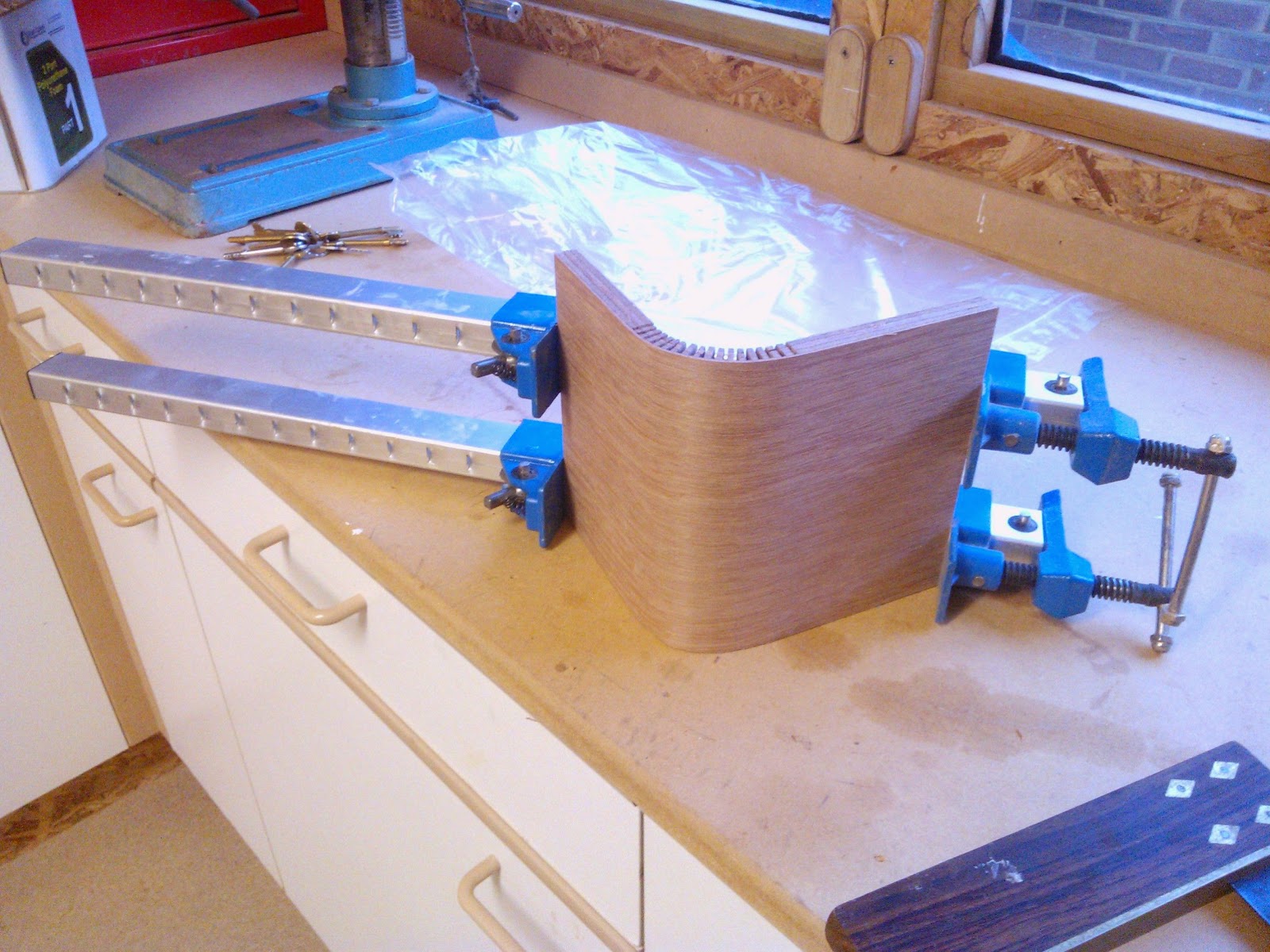
I thought initially i'd use the 1.5mm aeroply and it would just all fall into place yet after a week of cutting up much needed and costly materials i threw the towel in - panicked and nailed the piece to the jig and in the process destroyed the jig - very unprofessional.
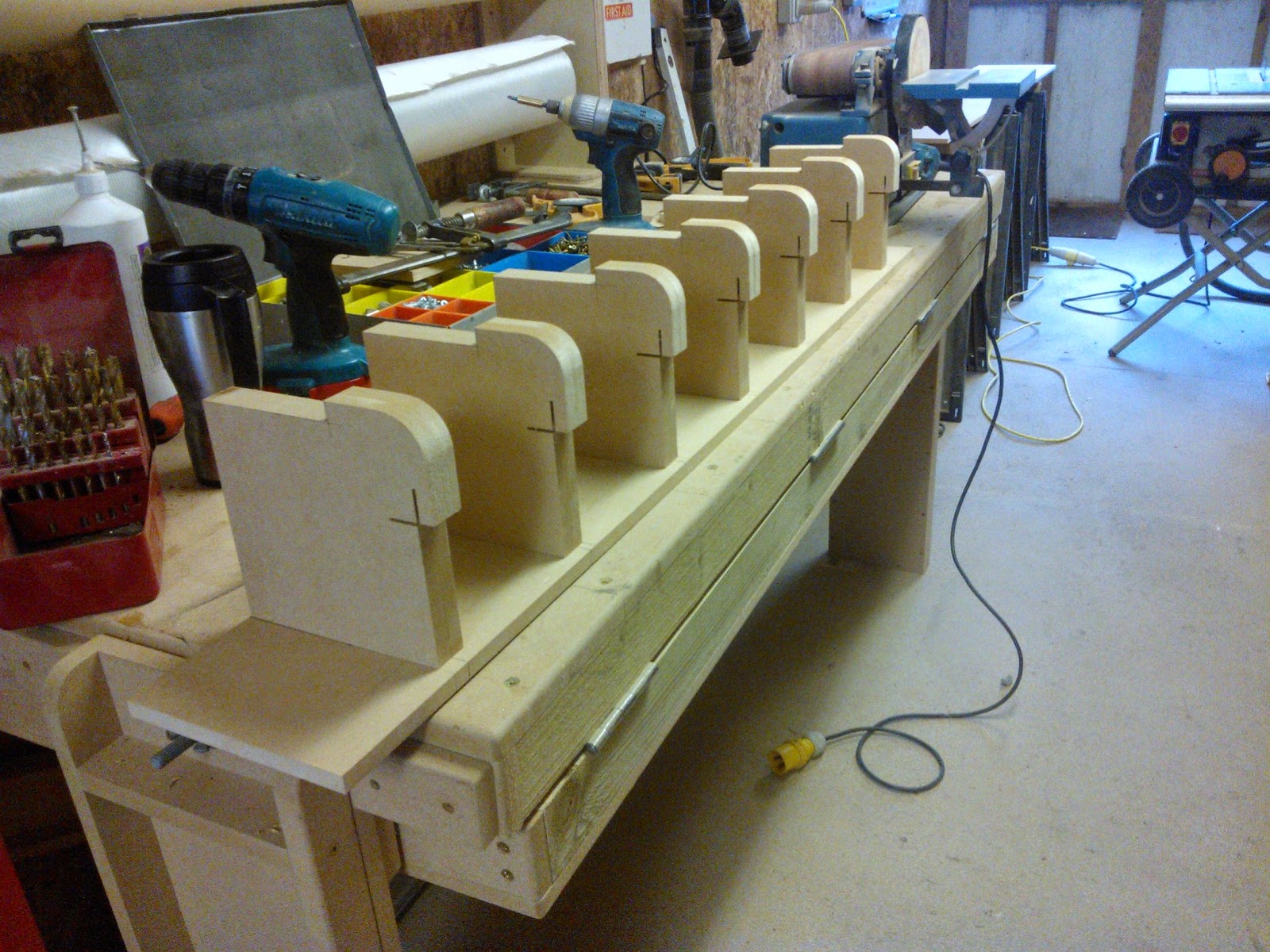
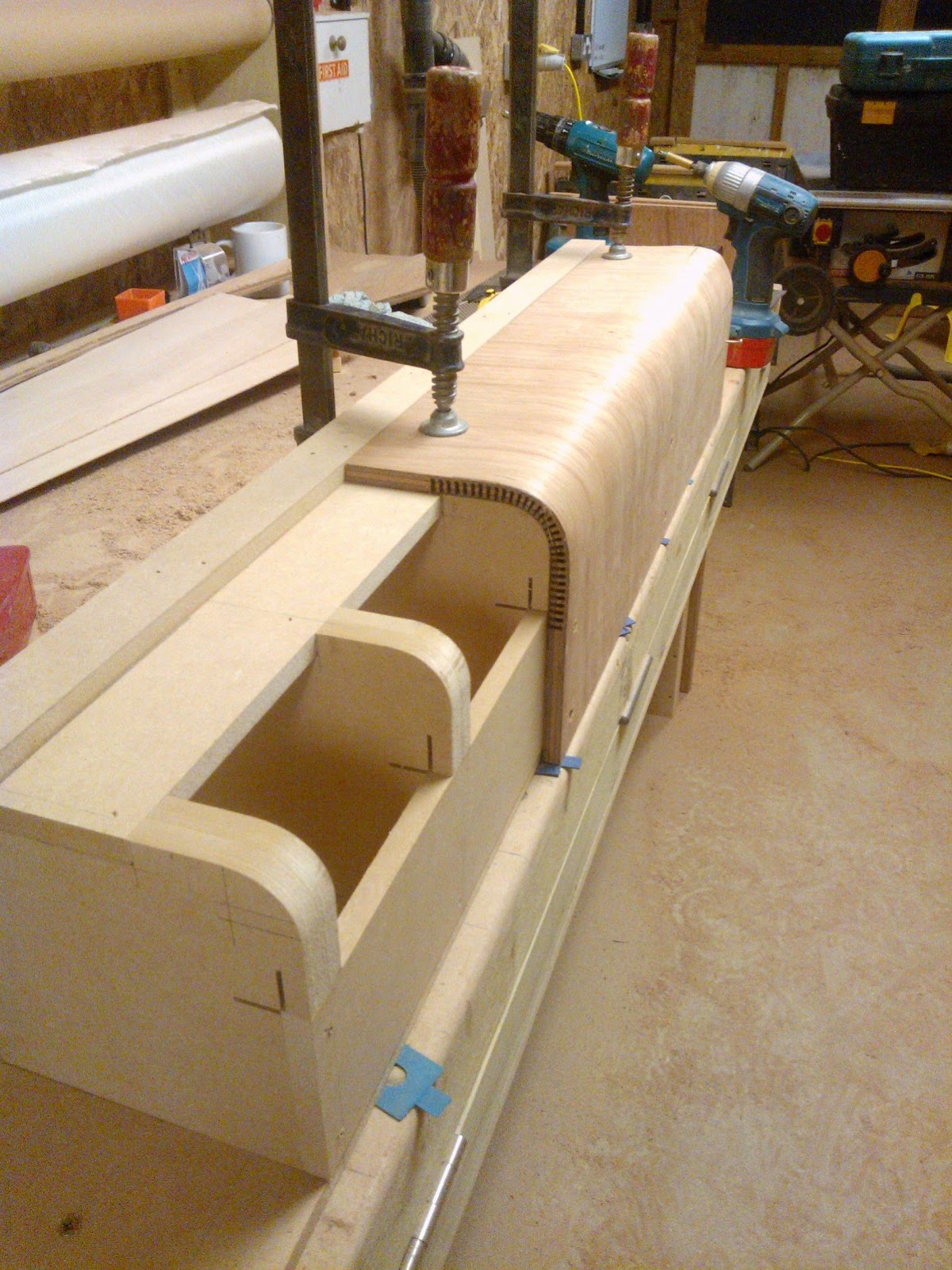
Now being a stubborn fucka if a guy can get a 4x2 around 90 degrees i sure as hell am going to get the ply to do the same thing. On my first attempt i realised grain plays a major part in supporting the curve, this after two days. I realised i need the exterior grain pattern running perpendicular to the direction of the curve, got that sorted - it now bends but how far?
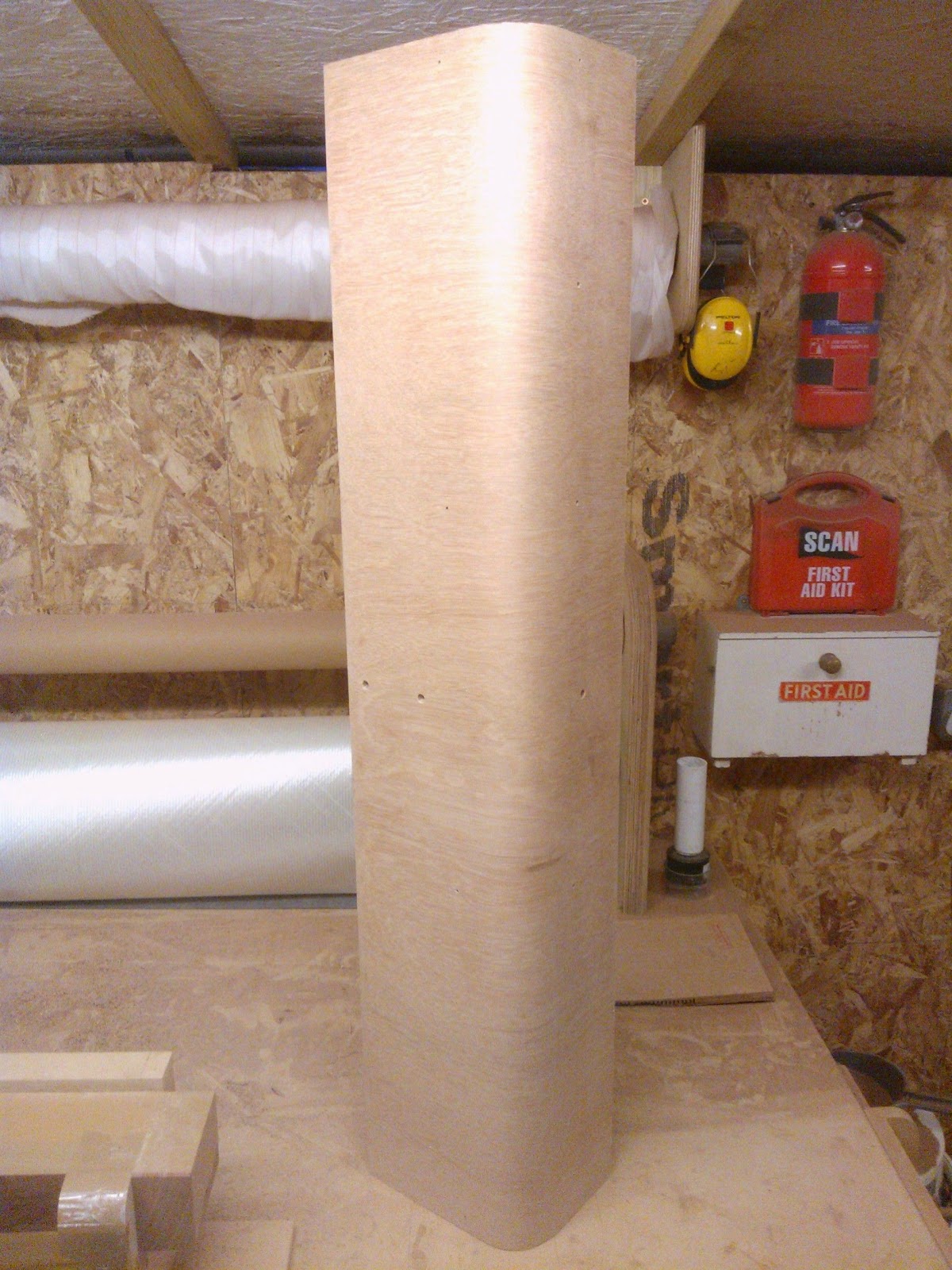
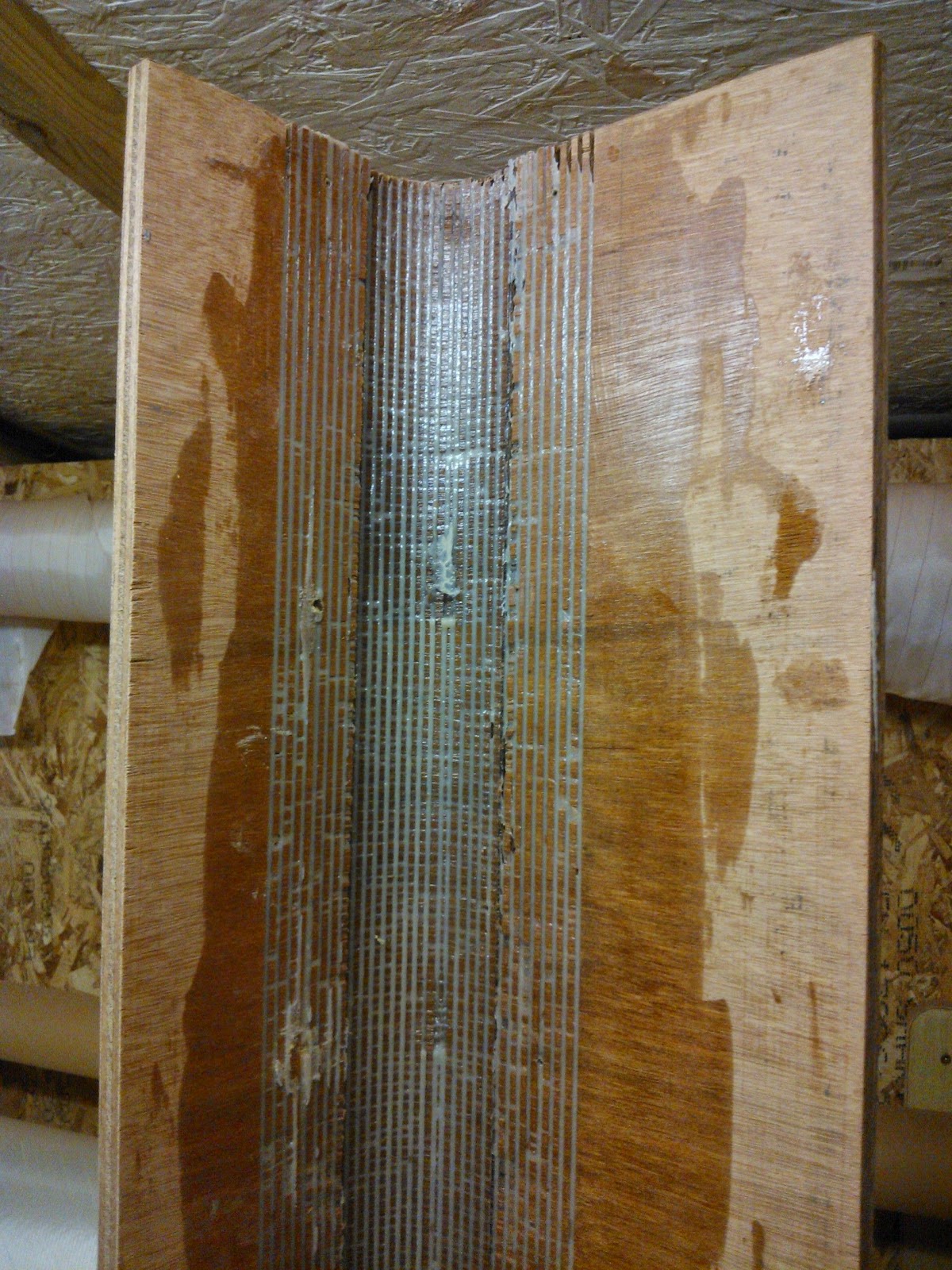
From this i wished i'd perservered with the main bulkhead a bit more as the flexiply is weak and so still need to add a hardwood post to the heads side to increase the bulkheads rigidity whereas if i'd made it from marine ply all be it kerfed they'd be more strength to the structure.
Happy new year!
Subscribe to:
Posts (Atom)