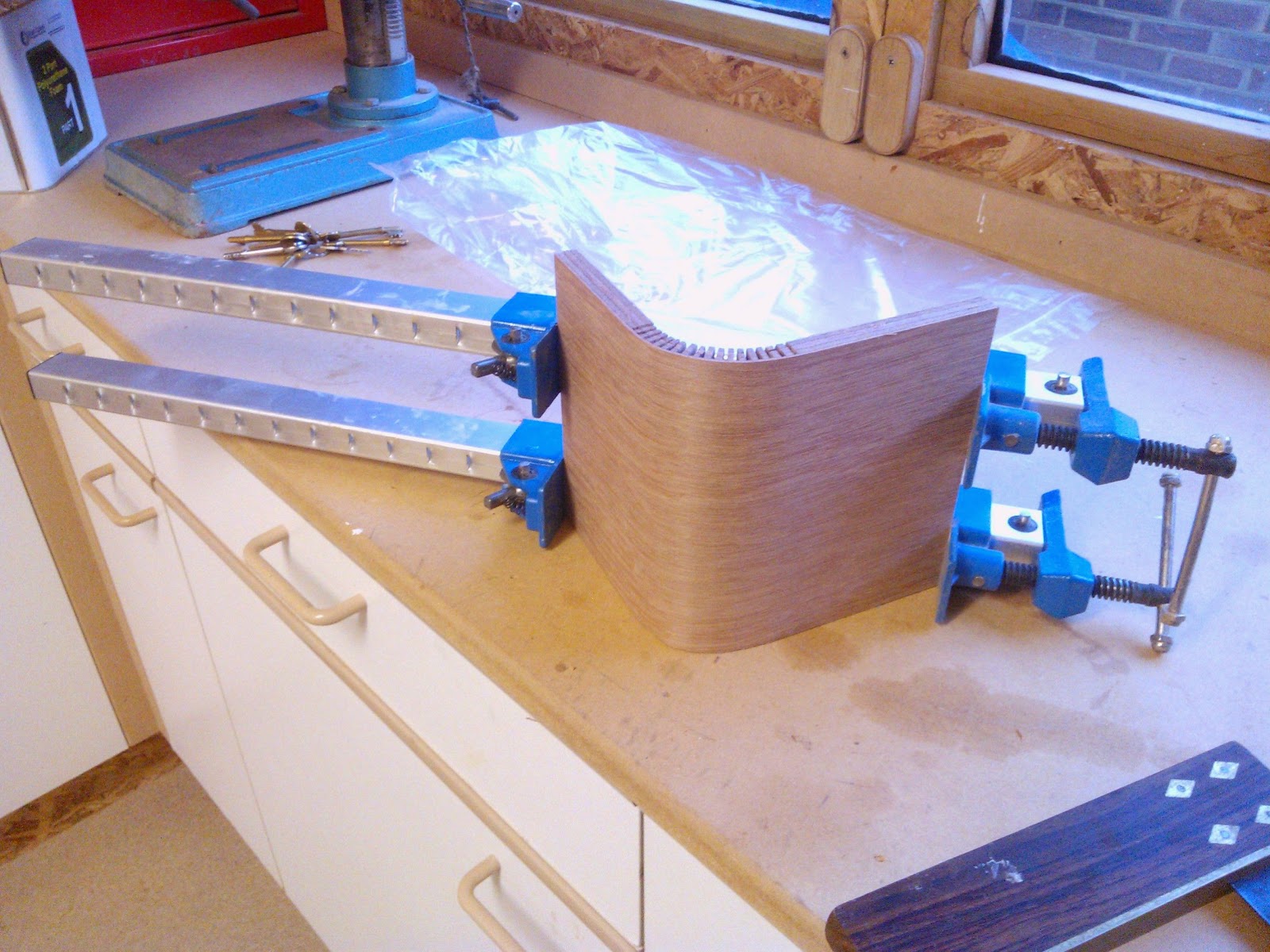
I remember the disappointment i felt when tackling the curved main bulkhead; nailing the flexiply to the jig after giving up trying to get the material to take the shape i wanted.
I thought initially i'd use the 1.5mm aeroply and it would just all fall into place yet after a week of cutting up much needed and costly materials i threw the towel in - panicked and nailed the piece to the jig and in the process destroyed the jig - very unprofessional.
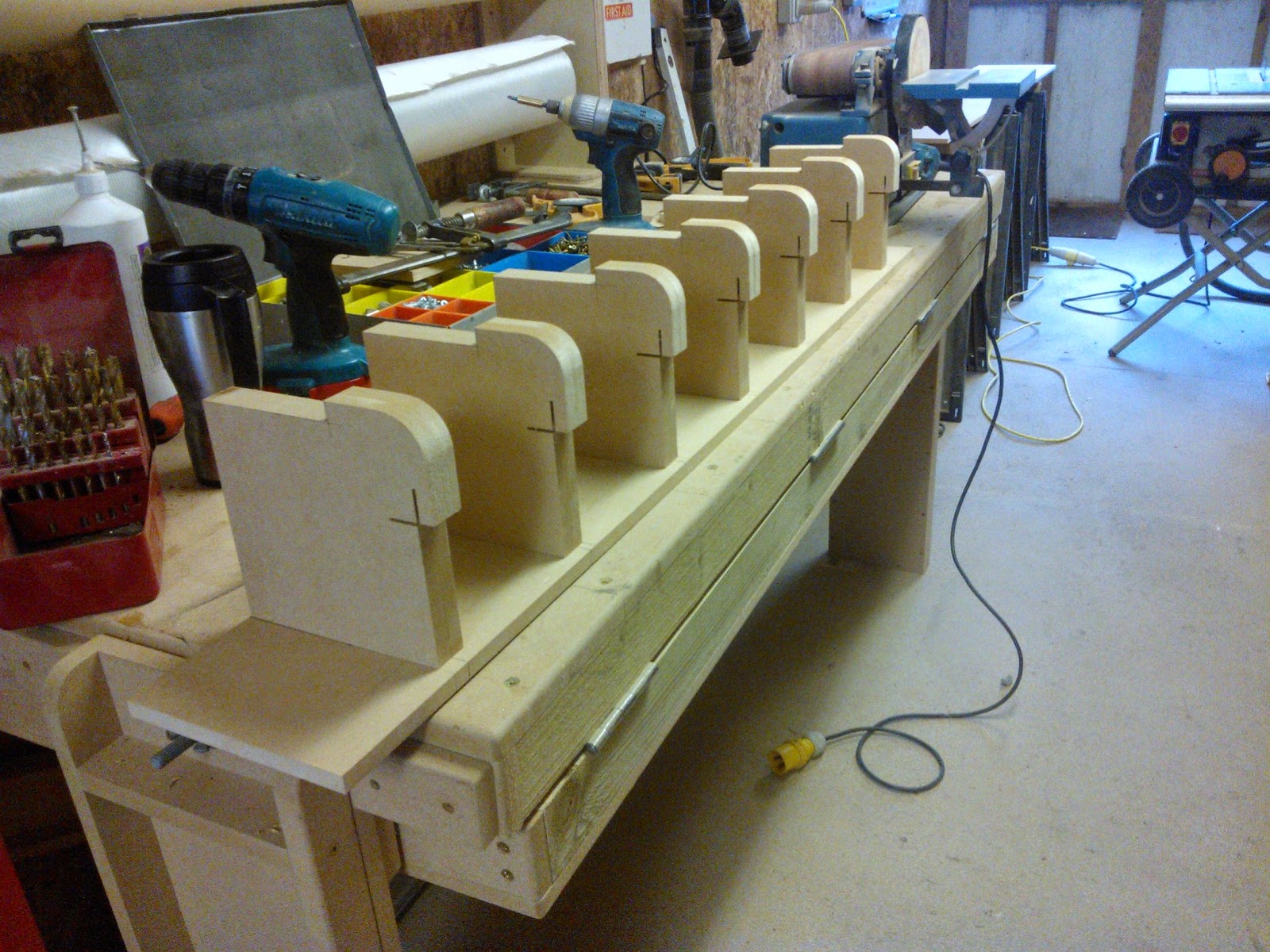
Still seeing as i want a modern-looking 'euro' interior to the inside the thorny issue of
getting ply to do what i want it to raised its ugly head, i was bolstered by an image i found whilst researching kerfing of a piece of 4 x 2 bent around 90 degrees which inspired me to have another go with a piece of 12mm ply with a certain degree of success.
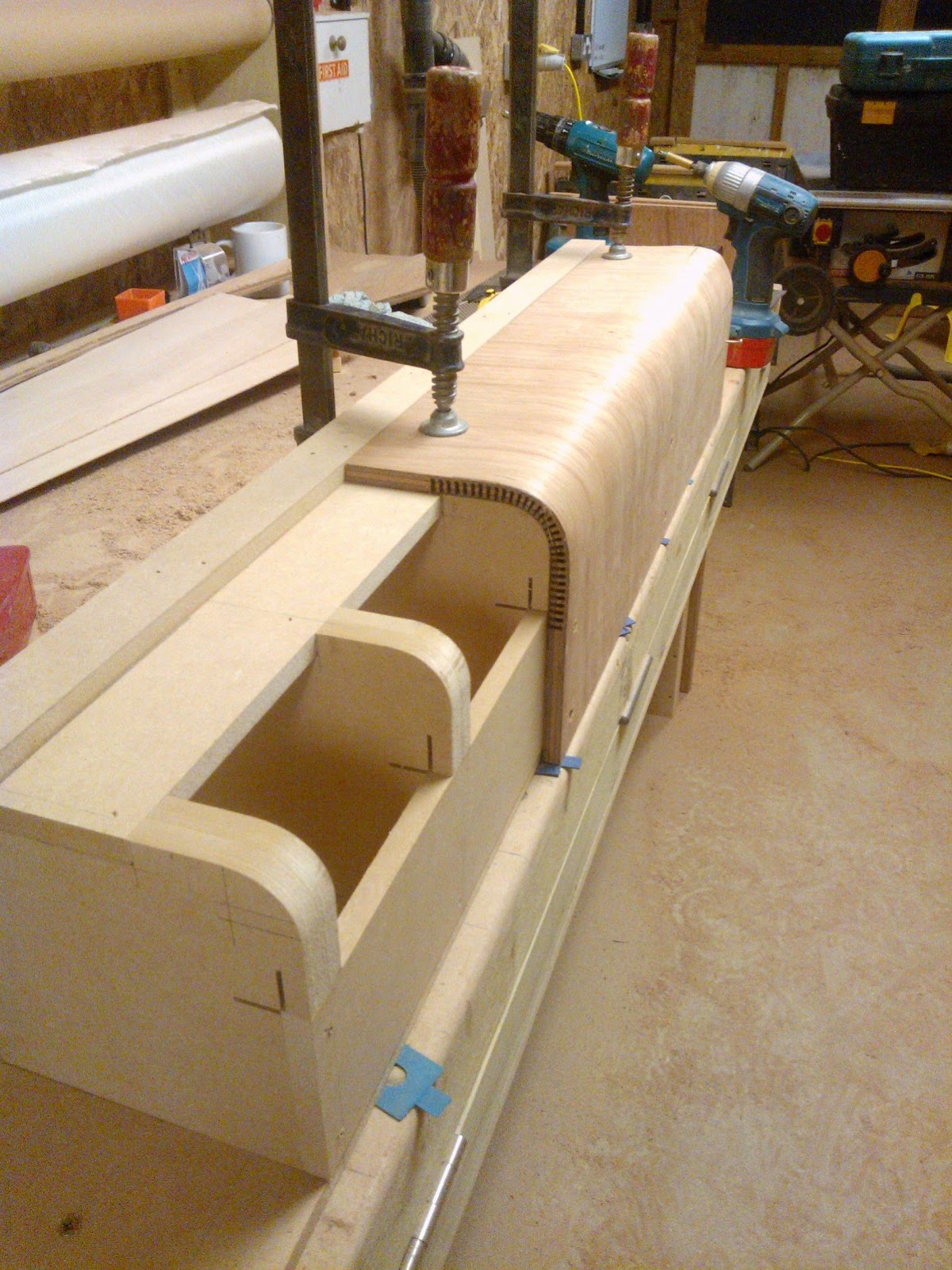
However after leaving it clamped for a couple of days little hairlines began to appear where the depths of each kerf minutely varied and eventually the test piece lost its shape and split.
Now being a stubborn fucka if a guy can get a 4x2 around 90 degrees i sure as hell am going to get the ply to do the same thing. On my first attempt i realised grain plays a major part in supporting the curve, this after two days. I realised i need the exterior grain pattern running perpendicular to the direction of the curve, got that sorted - it now bends but how far?
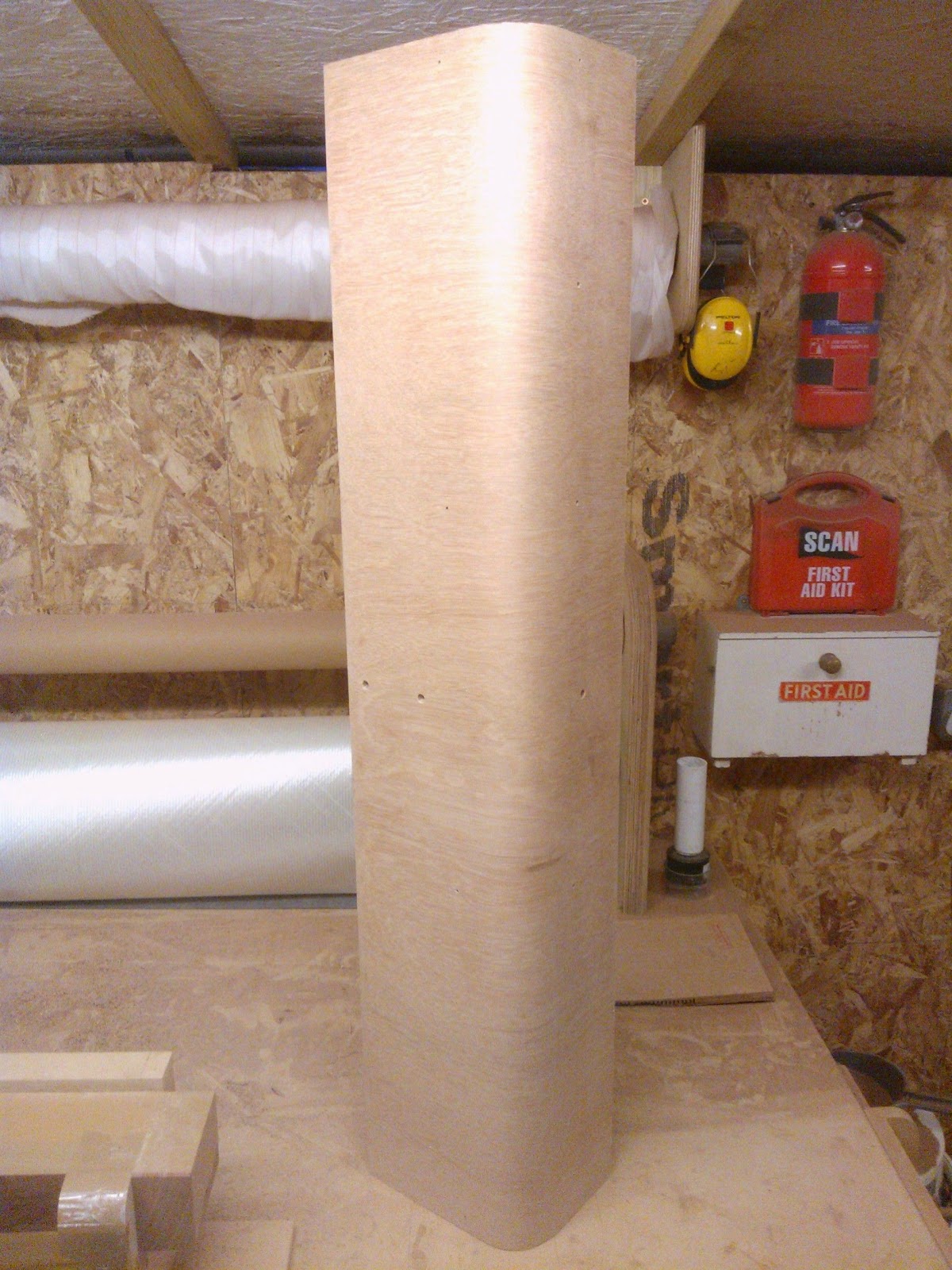
Got cutting and found a reasonable solution was the spacing of each kerf to be the width of the blade - all good but when i went to pull it into a 50mm radius one end bunched up, puzzling as when you google 'kerfing' it shows a simple process of evenly-spaced cuts within a couple of mil of the edge of the work piece and it takes the shape perfectly, for whatever reason this didn't work could be something to do with the fact it was ply and not solid, who knows, plus it wasn't so much a curve as a series of facets - no good!
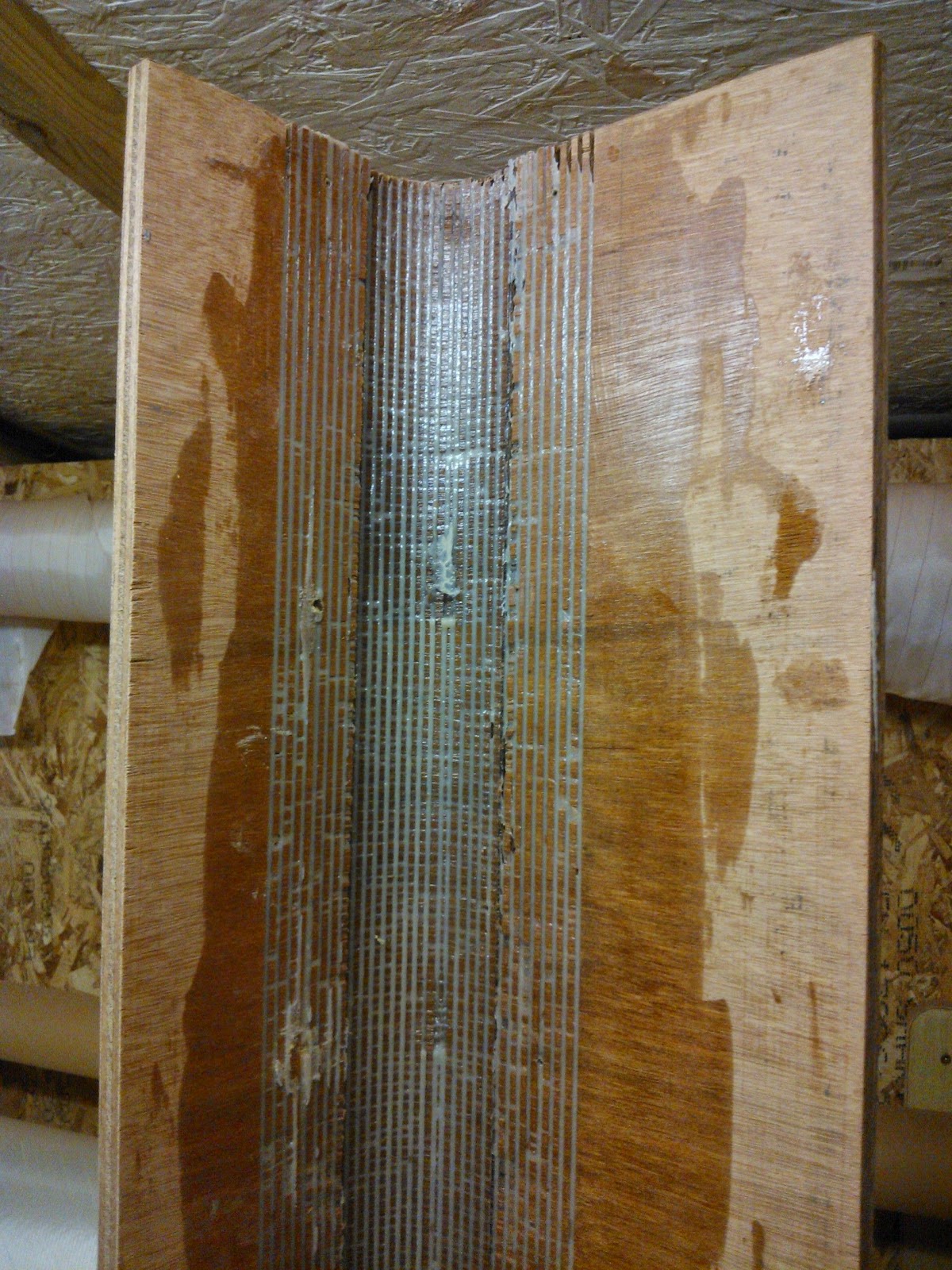
After chatting with brother Rik i routed out half the plys thickness on the inside of the radius, in this case 6mm and would you believe it the ply pulled down evenly across the jig although to maintain that i screwed through the work piece two hardwood battens one at the start of the radius and one at the end.
From this i wished i'd perservered with the main bulkhead a bit more as the flexiply is weak and so still need to add a hardwood post to the heads side to increase the bulkheads rigidity whereas if i'd made it from marine ply all be it kerfed they'd be more strength to the structure.
Happy new year!
Aha, always ask your brother! I'm glad you're making progress and hope the paid work is interesting and rewarding. All the best.
ReplyDeletecheers anon, yep repairing the current account as we speak, older brother rik (fellow woodsmith) knows a thing or two, think he paid more attention when the old man was learning us both in the ways of our craft.
ReplyDelete